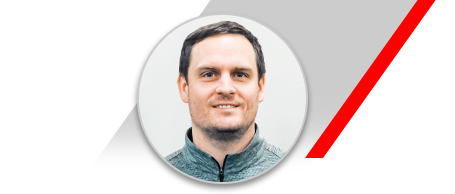
Creating a safe work environment is a top priority at Mazzella Companies. With regulations being regularly updated and the well-being of team members paramount, the role of Safety Director has taken center stage.
What led you to Mazzella Companies?
With 18 years under his belt, Kevin began his journey at Mazzella Companies as seasonal summer help in the shop after being recommended to the position by current team members and friends. “Some of my buddies worked here as well, like Joe Stanton, a Pricing Manager, and so he was kind of my team lead at the time so that helped me get my foot in the door.”

What inspired you to begin working in Safety?
Working part-time in the shop as well as attending a community college in the area, Kevin eventually began an internship followed by full-time work once he finished his degree. It was then that he began working with Mazzella Companies’ operations team, aiding in the development of standard operating procedures.
That eventually led him to onboard new companies with the IT team, making sure resources and processes were consistent across all units with business systems. Kevin shared, “That helped me get to know people outside of Cleveland, and when I transitioned to Safety about six years ago, I already had a lot of those relationships and familiarity with the sites from previous projects.”
Kevin explained that his hands-on experience in the shop and his process implementation and project management capabilities really helped point him in a direction where his talents could be best used. “A lot of what I do at work with my group is operations and service, so knowing a lot of how stuff is made, the inputs and outputs of each area, helps me understand the big picture and the importance of each phase along the way.”
Related: What Education Benefits Does Mazzella Companies Offer?
How has your position changed over time?
Growing into his Safety role six years ago, Kevin started without any official safety program in place at the time. “The majority of our sites did not have a lot of documentation or training in place for what we needed to be doing, because so many managers wore a safety hat on top of their day-to-day jobs.”
Building a standardized safety program gave Kevin opportunities to collaborate with team members throughout the organization in a quest to make a positive difference and adjust the mindset of what success looks like. “Rather than focusing on the number of incidents, we’re also focusing on what we are doing to prevent them. Whether it being through auditing, inspections, training, or hazard identification and mitigations. Because when you have people coming to work and going home healthy without injury or incident, it is better for everyone. You get to enjoy the day more, which leads to efficiency gains and an overall healthier work and life balance. Keeping safety at the forefront of everyone’s mind, and reminding each other to have a plan, and work that plan safely, helps reduce downtime and unwanted frustrations.”
With so much organizational growth over the last few years, Kevin shared that his current opportunity is building out best practices through a lot of information sharing and scaling those best practices so each location can utilize them. “We need to provide clarity to all team members and ensure there are readily available tools and resources to help teach one another about what we need to be doing and why.”
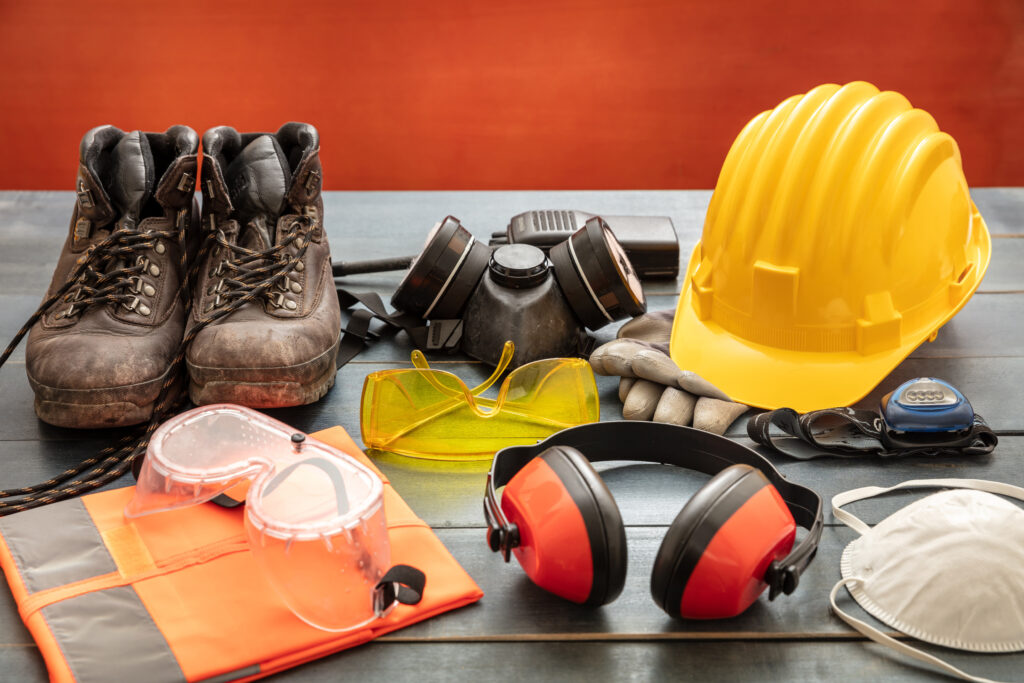
What do you believe is the role of the Safety Director?
Kevin said that his top priority is making sure every team member has what they need to work safe, with a mission in mind that each team member return home in the same healthy condition they arrived to work in. “We need team members to feel comfortable doing their work and empowered to address hazards or opportunities for improvement along the way. It’s also about making sure the managers understand their accountability in enforcing the safety and well-being of their teams and locations. We need to practice what we preach.”
Wanting to walk the walk and not just talk the talk, Kevin aims to set the example by making sure every team member has the right tools, jobsite setup, Personal Protective Equipment (PPE), training, is on an adequately staffed team to prevent a team member from working alone, and feels empowered with the ability to stop a job at any point due to safety concerns.
Related: What Personal Protective Equipment (PPE) Does Mazzella Companies Offer?
What is a project you are working on that excites you?
Kevin shared that one of the projects he is currently working on will help the team in getting collective feedback to improve, adapt, change, and reinforce risks – a Safety Committee. “As the company has grown, the Safety department has not. So, we’re trying to get more ambassadors within the organization in line with our safety program so we can get a larger group of people together to find out what everyone’s hearing and feeling to drive improvement.”
In addition to fleshing out the safety committee, Kevin shared that advancing the team’s technological tools is also a top priority. “Velocity EHS, an electronic system we can use to store all the Safety Data Sheets (SDS), is now in place in all locations. So, if someone is using a paint in a facility, we have the SDS at our fingertips.”
The next technological trajectory will encompass building out incident and safety management systems. In abandoning static documents, the team will have easy-to-extract data to better identify incident trends and make informed and evidence-based changes while maintaining on-demand compliance logs.
What is the biggest challenge facing the Safety department today?
One of the challenges Kevin shared was a lack of resources. “We don’t have the needed boots on the ground from the safety department in our locations to help drive execution and follow up, and some of our managers may not always be taking ownership and communicating regularly with their teams on safety expectations and then enforcing those expectations.”
On top of resources, Kevin shared that with so much growth, and so many moving parts, shared priorities have become another challenge. “We want continual communication, awareness, and acknowledgement of safety in the day to day to help establish a culture of safety. It’s hard to say we have a culture of behaving safe when we may not be using equipment as intended or not wearing the proper PPE. How we perform when others aren’t around is a true reflection of our culture and right now, we may walk into a place and there’s no visual workplace or there may not be any designation on workspace versus walkway space. Really all locations should be audit ready at all times. We want to encourage customers and visitors alike to tour our sites any time and if a site or department isn’t talking about safety and making it important to their teams, then they’re opening themselves up for issues.”
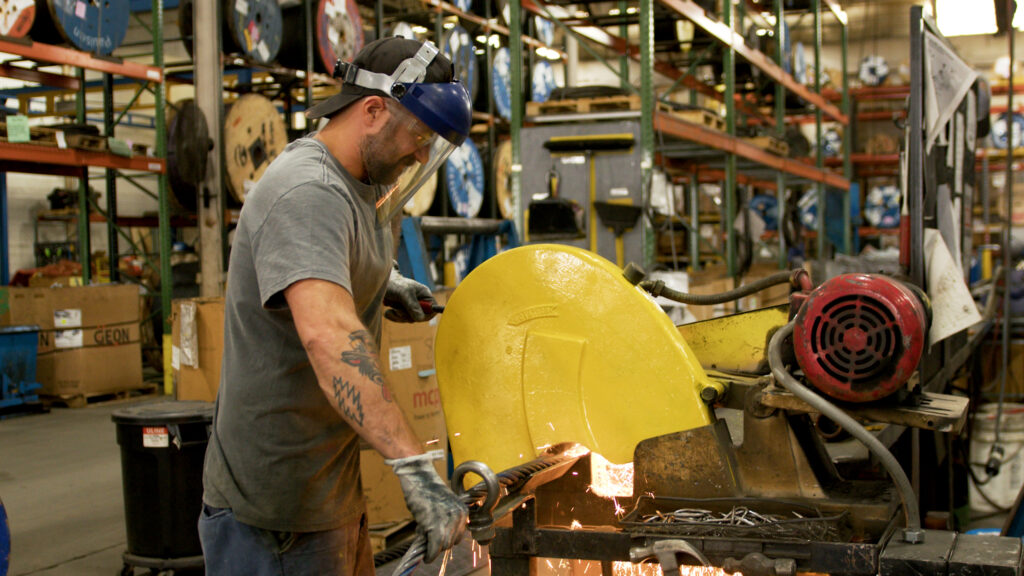
How do you stay connected to team members around the country?
Outside of regional and tactical meetings and daily and weekly huddles, Kevin says, “We’re putting content out there in different forums, i.e., a monthly QSTR Update, a Stay Safe monthly training, safety talks and safety alerts that go out weekly, and consistent auditing to identify trends and areas for improvements.”
Kevin said that traveling to individual site locations is also important as it keeps information flowing both ways. “We have visitors at sites all the time, not just from QSTR, and we utilize those other team members to relay information we may hear from local fire departments or our insurance groups that are routinely checking in at certain locations.”
How do you stay on top of laws and regulations that apply to your industry?
Kevin shared that as he is a representative of Mazzella Companies on a safety council the company belongs to, he hears a lot of what is coming down the pike. In addition, he uses a software called Techstreet that sends out alerts when standards and regulations are updated. He also receives regular communications from the Occupational Safety and Health Administration (OSHA), which is crucial for staying up to date on federal and state guidelines.
Kevin said, “It’s almost information overload at some points, but once you sift through, you can start to see trends and understand the ‘why’ behind the changes. It’s not just standards, it’s also the bigger part of moving safety forward. OSHA regulations give us the minimum requirements to meet, and in several cases direct us to the manufacturer’s guidelines for further clarification. However, there are cases where we may become more stringent in designated areas in order to prevent an incident trend and keep people safe.”
What awards or certificates have Mazzella Companies earned in Safety?
Kevin said that on the lifting side of the business, Mazzella Companies belongs to Associated Wire Rope Fabricator (AWRF), a trade association, and each year safety statistics, such as number of team members, injuries, injuries that required medical treatment, hours worked, and off time or light duty are submitted and compared with others in the industry. “We’ve received a couple platinum awards from that association which is a positive indicator that we are heading in the right direction.”
Outside of industry awards, several states have awarded certain locations for maintaining an accident-free workplace, be it through a state funded program or local chamber of commerce. “We have also earned some customer awards, often times when working a designated number of hours at a jobsite without any incidents.”
What professional podcasts or books can you recommend that have helped you on your career path?
Kevin recommended a podcast by Dave Ramsey called The EntreLeadership Podcast that he enjoys listening to while traveling, and also recommended a book called Atomic Habits by James Clear, and Make Your Bed by William H. McRaven. “The overarching theme about each book is about improving yourself, building right habits and becoming more effective, which then translates to bettering those around you and ensuring there are wins each day. Sometimes in life, especially the safety world, you may only hear about the things that go wrong. But I feel it’s important to maintain perspective to recognize and reinforce the positives throughout the day.”
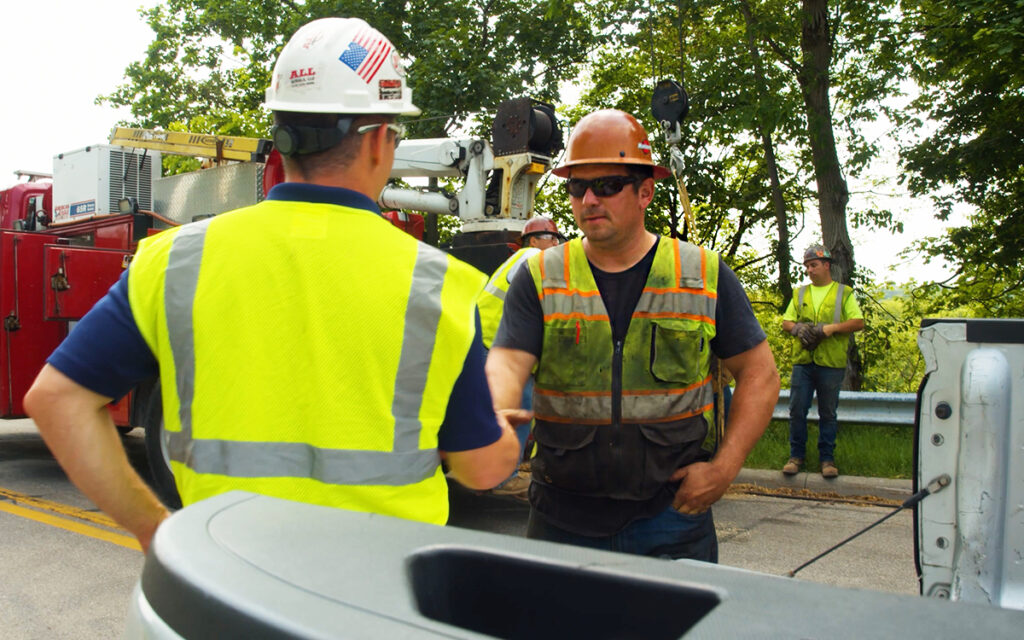
What advice would you give someone looking to join the Safety team?
“You have to be willing to learn, understand change management, be willing to speak up as situations require, and want to work with people to understand how to navigate risk. If you’re looking to be at your desk all day and get in a routine of doing the same thing over and over, you’re probably not going to be happy in a safety role.”
Kevin went on to share that being able to empathize with others is also necessary. “When things go wrong, there’s a human element to it. It’s not just about who did what wrong. There are always going to be both human and system elements involved. It’s about figuring out where the breakdown occurred, so corrections are in place moving forward. Not everyone wakes up and thinks about the intricacies of a safety program, so we always need a good balance of being part developer, teacher, and enforcer for team members.”
Sharing the Safety Perspective
Since Kevin started 18 years ago, he has had a family and has watched many of his teammates start families. “It really crystallized in my head about the importance of care and concern for the team to ensure we are all working smart and going home in safe and healthy conditions. Having that perspective helps me realize that while we’re all in it to win, we can’t do that if someone is hurt. We need to make sure we do what we need to do, safely.”