At Mazzella Companies, every role and the team members who fill it are vital and unique. Each ensures the seamless delivery of our products and services.
A vital function of the logistics chain is Shipping and Receiving. To shed light on the sometimes unseen efforts that keep our operations running smoothly, we spent the day following Kaleb Sullivan, a Shipping and Receiving Coordinator at Mazzella Companies’ Distribution Center (DC) in Memphis, Tennessee.
“I was the first full-time hire when we opened the DC here, and we only had half of the building we have now.”
What does a typical day look like?
We find Kaleb overseeing a delivery truck coming in. “We’re about to start breaking that apart, getting that put into its locations, and getting that set up so that the guys will be ready to pick it up in the warehouse.”
Kaleb says that a typical day in his role consists mainly of monitoring the status of orders and walking the floor to ensure everyone has what they need to succeed. He and his team are always thinking about the next steps and how to be more efficient.
Daily Shipping and Receiving tasks:
- Loading and unloading trucks as required
- Reviewing and interpreting part numbers
- Inspecting and verifying delivered products
- Pulling inventory for orders and replenishing stock
- Scheduling shipments with outside carriers
- Ensuring all orders have been printed
- Monitoring the status of orders from pending, picked, and shipped
- Confirming the team is on track to complete the day’s orders
- Checking that the customer is billed for what’s shipped
- Spot-checking for back orders that have come up
The typical weekly flow for Kaleb starts on a Wednesday and moves through Tuesdays.
“We get approval for all of the warehouse orders on Wednesday, so when we come in Thursday, we’ll print all of those and print all of the labels. Then, the rest of the time, we’ll be trying to get those pushed out and to the customer. So, by Tuesday, we’re normally hitting the point that we’re clearing out most of those orders and will be just spot-checking to make sure no backorders have come up.”
As a Shipping and Receiving Coordinator, Kaleb coordinates between the national corporate sales and manufacturing teams and everyone at his Distribution Center in Memphis.
He plays a particularly crucial role for a high-volume customer with various needs. “What that customer orders will go to their warehouse and then anywhere from baseball stadiums to military bases.”
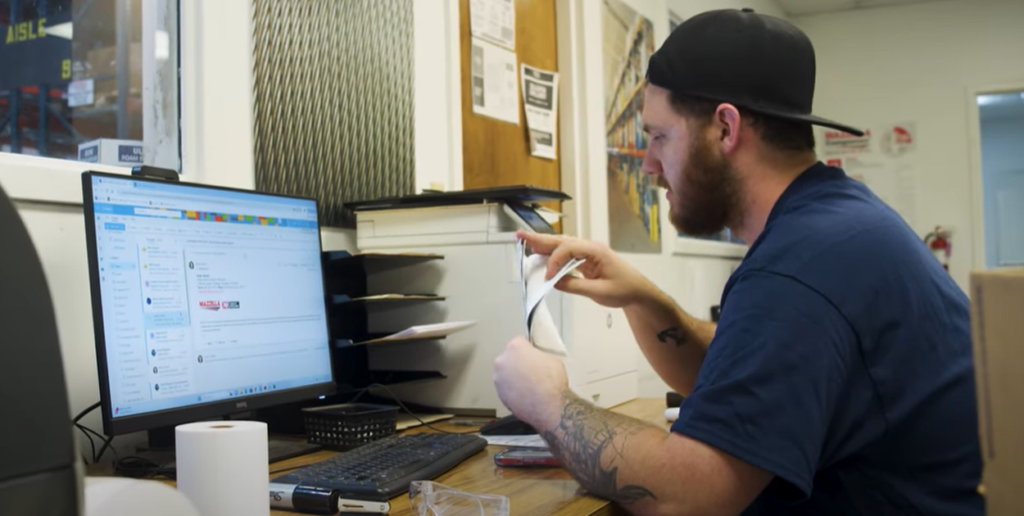
What equipment and skills are required for this role?
Each role at Mazzella Companies is unique regarding the equipment used and the skills needed to be a successful team member.
Required Equipment
Computer-Based Equipment:
Microsoft Office: The company uses Outlook and Teams to stay connected and offers organizational tools such as Word, Excel, Access, PowerPoint, and OneNote to keep organized.
UPS Worldship: This system generates shipping labels, estimates shipping costs, schedules pickups, and tracks shipments.
Enterprise Resource Planning (ERP) System: This system is crucial and used to track inventory levels in real-time, process orders, schedule shipments, generate shipping documents, track supplier performance, and generate reports.
Mechanical Equipment:
Forklifts: These are used to move heavy pallets of goods around the warehouse, onto trucks, and off of trucks. Certification is not a prerequisite, and all team members will be qualified users after completing our training program.
Pallet Jack: These are similar to a forklift but are smaller and easier to maneuver. They’re used for moving pallets short distances.
Scissor Lifts: These are used to raise or lower goods to a comfortable height to reduce the risk of injury.
Scales: These are used to weigh goods for shipping. Accurate weights are essential for determining shipping costs and ensuring trucks are not overloaded.
Calculators: These are regularly used to calculate the total weight of a total or cost of a multi-item shipment, estimate storage space requirements, or convert measurements.
Kaleb said that while his role as Coordinator means he doesn’t often unload a truck, having the training is priceless. “There are still times when I’ll unload and load a truck, so I know how to operate just about any equipment used for material handling.”
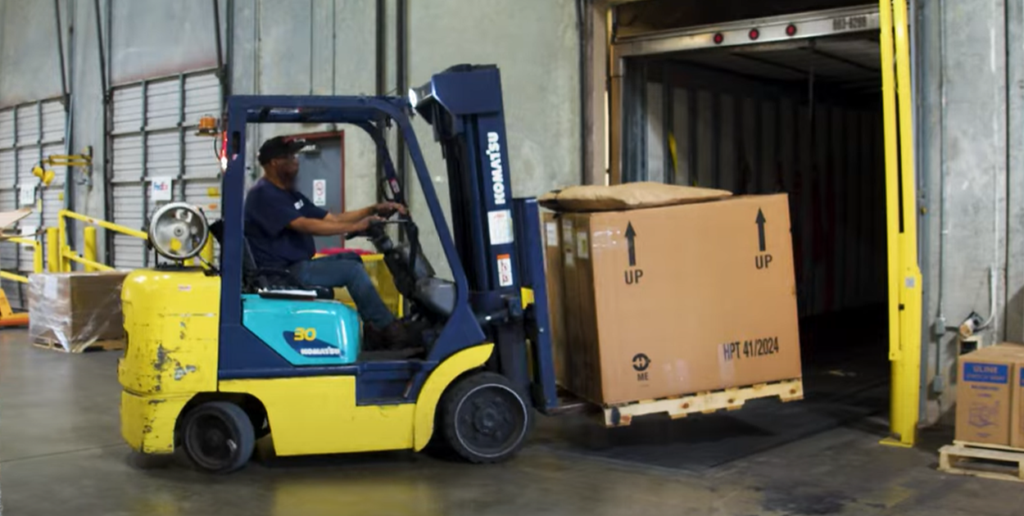
Required Skills with Examples:
- Written and Communication: The person in this role might need to email a supplier to clarify the delivery schedule or communicate with a customer about a shipment delay.
- Mechanical Aptitude: The person in this role may operate machinery like forklifts or pallet jacks. They will also need to understand how to handle and store different types of goods safely.
- Conceptual Planning: The person in this role will help organize the warehouse layout for efficient storage and retrieval of goods. This includes planning the loading and unloading process to minimize damage and maximize space utilization and scheduling deliveries to meet customer deadlines.
- Problem-Solving: If a shipment arrives damaged, this role would need to figure out the best course of action, such as returning the goods to the supplier or arranging for a replacement.
- Lifting and Pulling up to 50 Pounds: Many tasks in shipping and receiving involve physical labor, such as loading and unloading trucks, moving goods within the warehouse, and packing items for shipment.
- Detail-Oriented and Disciplined: The role might need to carefully check the part numbers of items received against the purchase order to ensure accuracy.
- Ability to Decipher Similar Part Numbers: Our company deals with many different types of products. Being able to quickly and accurately identify parts based on their numbers can help prevent errors in shipping and receiving.
- Process Improvement Mindset: This role might notice a recurring issue with shipments from a particular supplier and suggest changing the ordering or receiving process to prevent future problems.
Kaleb emphasized the importance of mechanical aptitude and problem-solving in the role. “We have so many different things that require solutions, so there are times that we’ve had to be creative and build something to store them.”
Kaleb’s first role at Mazzella Companies was as a Shipping and Receiving Clerk. Learning to pick, pack, and ship things took time, but he always took every chance to learn something, especially the products.
“I was given the opportunity to do the rigging inspections, which means going to the customers, inspecting the rigging equipment they’re using, and determining whether it’s still safe to use or if we need to replace it. So, I learned a lot about how our items were used, what can cause damage to them, and what is the best way to use them.”
How do you stay organized and efficient?
While Kaleb and his team unpack the truck, Kaleb organizes the products so they’re easy to pick up and get out. “When we run out of room in the aisles, we’ll put them on this end cap here, so everything is still close together and relatively easy to pick up.”
The warehouse itself is set up so that orders are stored in and eventually leave from the same places to go to the same distributors, with parts of the warehouse dedicated to specific customers.
Kaleb shared that all rigging hardware and parts must have some form of identification, such as the manufacturer’s name and a working load limit. So, every piece must be stamped with the size and/or working load limit to be appropriately grouped for orders.
Learning the products was essential to Kaleb’s organizational success, which he showcased by going through many of the products’ intents and purposes. “Knowing what the products are intended to do is very beneficial. It’s not something you have to have, but a lot of times, it’s helpful just to know what you’re looking for. If you’re looking only at the part number, you could get confused because part numbers can be very close, but having the knowledge of what it does will help you identify the part you need.”
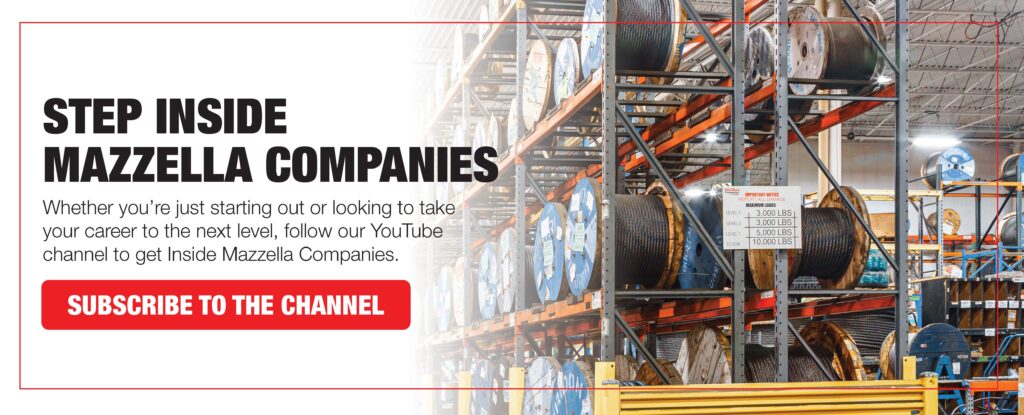
How do you stay connected?
Staying connected at Mazzella Companies is not just a catchphrase – it’s a daily practice that drives our operations.
At his team’s daily huddle, they review their production and standard On-Time Deliveries (OTD) and safety requirements for the day. They also discuss other topics that need to be addressed with the team, like on-site events or customer tours.
“A lot of my meetings are just progression updates. We have a daily huddle with all of the DC team, which is coordinators and managers, to go over the backlog, making sure that we’re staying on top of back orders.”
Kaleb explained that he has three huddles every day. A daily huddle with the DC team, one with their distribution manager to go over OTD, other KPIs (Key Performance Indicators), and safety requirements, and then a customer daily huddle to communicate what’s going on that day in the DC and go over any issues that they could foresee coming up or problems that they’re in the process of solving for the customer.
Kaleb explained the importance of the OTD status, “Every sales order has a load date that goes with it. If we ship on or before that load date, our OTD status will stay at 100%. If we have something back-ordered, then our OTD will take a hit.”
What are some of the challenges in your role?
One of Kaleb’s favorite parts of his job is always coming up against a challenge. “We have many things that we have to balance—it’s not just getting orders out. There’s always something to work towards and improve on.”
That process-improvement mindset was especially useful when transitioning to advanced shipping. “The notice criteria weren’t meeting our customer’s needs, which has been an ongoing battle of figuring out what the new parameters are and finding the solution that works best. We are always improving that process.”
Sometimes, challenges can be presented in their inventory that is not 100% accurate. “For the volume that we’re shipping out and the amount of people we have, we’re still building that, which is a big challenge because the customer I work with is very particular about when things ship and knows how quickly they can expect something.”
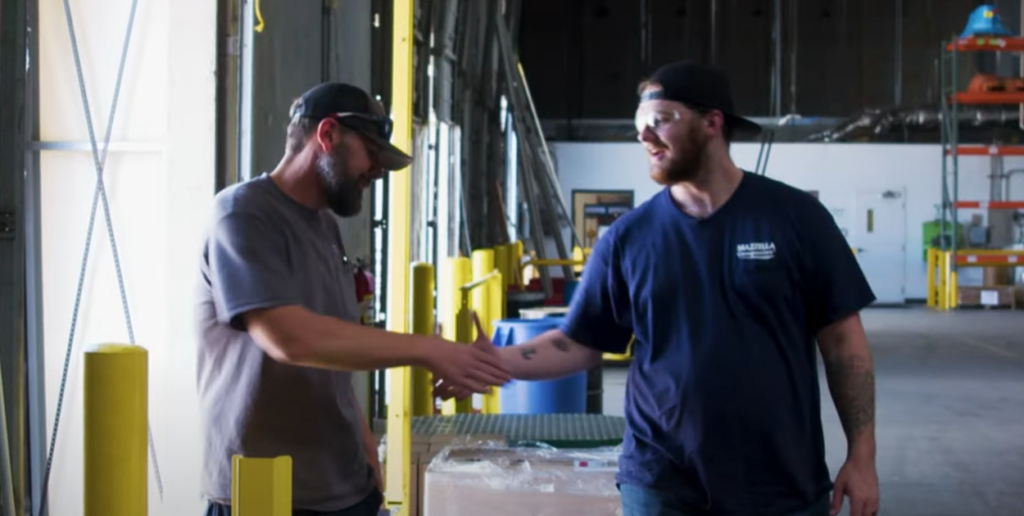
Why Mazzella Companies?
Kaleb said that one of the main things he loves about Mazzella Companies is that the Company is constantly growing. “I mean, 70 years, and we haven’t stagnated. We’ve continually expanded and grown, and there’s always an opportunity to learn something new and go somewhere new.”
Kaleb started his career in logistics before even graduating high school. “I was initially recruited from a career and technical center where I learned supply chain management and logistics.”
Kaleb described his experience at the school, which was, in reality, a functioning third-party logistics warehouse for a company that distributed books to underprivileged children, and his time as a FedEx worker as invaluable. “I’ve always had some kind of hand in distribution.”
Kaleb says that having the DC is a strategy that gives the organization more opportunity for production to make custom-manufactured solutions. This means mass-produced orders can be in stock and ready to ship versus made-on-demand, which helps meet business demands and encourages growth.
What advice would you give a newcomer?
When Kaleb started, he was the only full-time team member, and he suggested that newcomers always ask questions that help them learn more about the business and stay hungry.
“One of our core values here is to stay hungry. So, coming in, asking questions, wanting to learn more about the production process, continually wanting to know more will propel you a lot further in this company.”
As a new team member, he wanted to learn more while they were still in the setup phase and had the time to learn. He spent time interning at another Mazzella Companies location, understanding the manufacturing process for wire rope slings and sewing synthetics. “I learned a lot about the customer base that we were serving to then.”
More than anything, Kaleb says that practice is the key to success for a newcomer. “It’s getting your reps in, continually doing the same task over and over to make sure that you have executed it to the best of your ability.”
Fueling Our Momentum
After a day in Kaleb’s life, it’s clear that his role is demanding and essential to our operations. His story highlights the exacting nature of logistics and a commitment to excellence and continuous improvement. At Mazzella Companies, it’s the dedication of team members like Kaleb that fuels our momentum, propelling us toward a prosperous future.
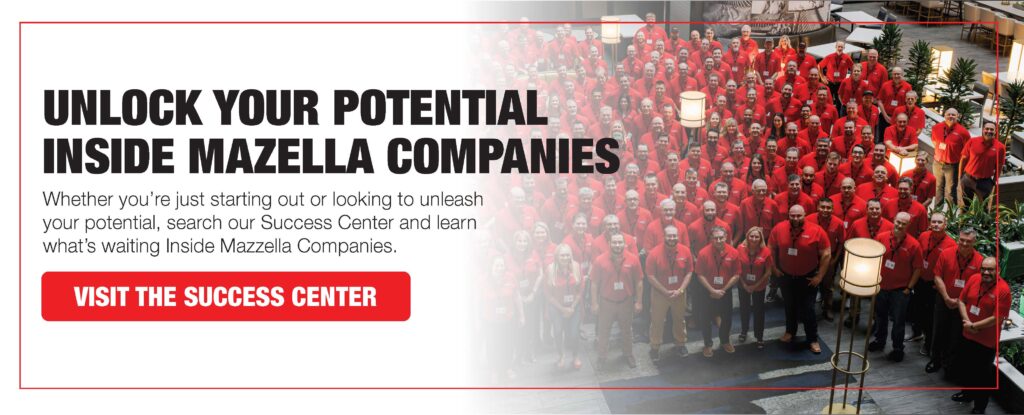